This was a tough lesson learnt, I was approached by the customer if i could help them look at some Rhodes they want to buy, I said, why not if you are willing to pay for the time I will do that. When I arrived the sight was pretty dire, broken keys, missing tone bars completely rotten case. I told him, it can be saved and made playable and gave him some cost estimate, what I didn’t expect was he came back and said well all the gear I have is in A+ shape, could you make this one also A+? I should have said at that point that we better pick better candidate to turn it into A+ instrument but the challenge was on.
I enjoyed some good old school key bed ironing just to find out I couldn’t find any key tops the right size to fit Rhodes, so I had to individually file them to size one by one. Slow and steady was the key to success.
its a slow but rewarding process

Next step was to tidy up the rest of the key bed, put new cashmere into some of the key bushings and adjust others to ensure it all fits well. Little I knew what devil was in play there. It was 1980 Mark II and I’m to this day not sure if it was from the factory or some play of time, but nearly every key had a different number and was made from different piece of wood therefore warping massively each in a different direction. I had to remove the hard wood blocks at the end of the key and mill it to make it not stick and interfere with each other. It was impossible to have both the key pedestals flat square and uniform and front of the keys. they were too badly twisted to achieve that so I had to make some sort of compromise. Next steps were routine installation of miracle mod, new hammer tips and damper felts. There was about 8 hammers in the middle which were so worn I had to replace them.
Next thing to look at was the harp, the oversize Vintage Vibe grommet screws were a real life saver here because original screws were already so loose it wouldn’t hold properly, I was amazed at the sheer amount of sustain this change brought. I went for full set of grommets screws washers and springs and the transformation was definitely worth it.
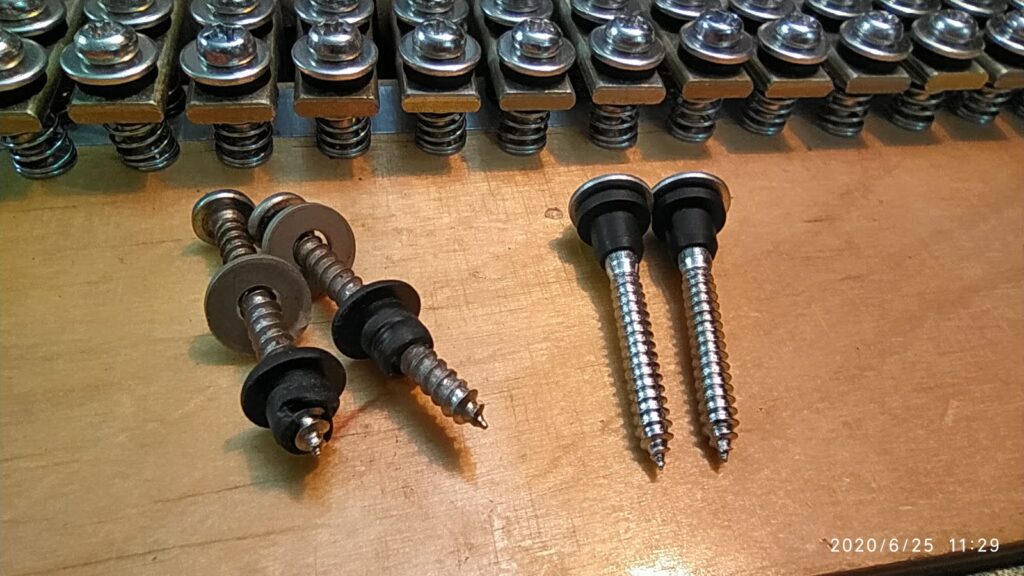
Next thing to do was the cosmetic aspects. I personally was shocked to find out he chose the country western style Tolex to go with, but at the end it kind of grew on me when he mentioned the part of the idea to dedicate it to Clint Eastwood and make a new sub panel. I had the legs sent to be re chromed, added Vintage Vibe pedal rod, Sand blasted and powder coated the pedal, made new couplers on the lathe and had the top cover repainted to match the rest of the piano combining the shiny chrome and cowboy leather.
Hardest part was to get rid of the double strikes at hi velocities. The root cause was too much wear in the hammer comb/ hammer bushing making it even more bouncy then usual. I for sure know it would have been easier to start with nicer instrument, but it was epic journey with happy end. I had to readjust the key bushings once more when the piano settled in its new home, different moisture and temperature made it warp a bit more and some of he keys became sticky.